Century West Engineering has been working with City of Auburn (City) staff at the Auburn Municipal Airport since 2012 when we were hired to update their Airport Master Plan (AMP). The major project that resulted from that effort was the Runway 16-34 extension, which wrapped up construction in 2020. While that project was in development, Century West Senior Project Manager Greg Reince, PE and Auburn Airport Manager Tim Mensonides, CM were already looking forward to future projects.
In 2018, the Washington Department of Transportation (WSDOT) Aviation Division published a pavement report that identified the existing Auburn runway as having poor pavement condition that warranted major rehabilitation, i.e., an overlay or reconstruction. At that time, a runway rehabilitation was not programmed into the Airport’s Capital Improvement Program (ACIP), which is a requirement for receiving Federal Aviation Administration (FAA) funding. Century West led a successful campaign with the FAA to update the ACIP so that the runway rehabilitation was eligible for funding in 2023.
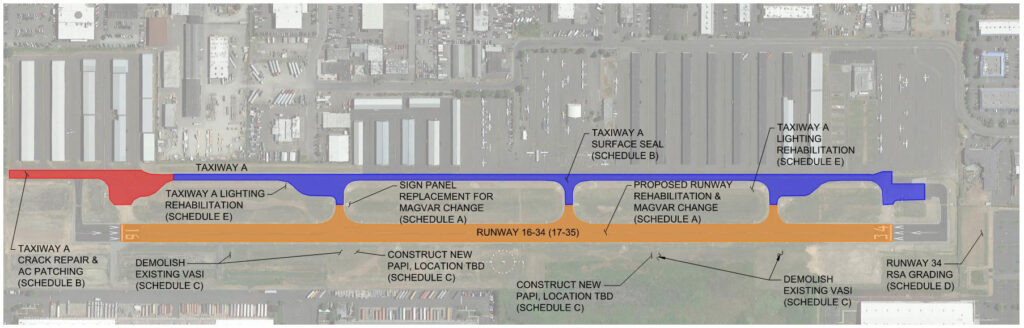
Design began in June 2022 and proceeded quickly despite a few unique challenges. The existing runway had an offset crown, which meant that the highest point of the runway was offset approximately 10 feet to the east. This conflicted with FAA regulations that recommend the crown to run along the actual pavement centerline. To further complicate the crown issues, the runway extensions that were constructed in 2020 had crowns placed at centerline. As a result, the match from the existing offset crown to the new runway extension crown at centerline resulted in a “hump” along the grade that would be corrected with this project. To correct the crown issues while minimizing construction costs, the Century West team had to design a plan for the mill and inlay of new pavement at variable depths along the cross-section. As the existing asphalt was only 5 to 6 inches deep, this required a significant amount of fine-tuning to achieve the desired 1% to 2% cross-slope, no more than 3-inch maximum mill depth, and a variable inlay thickness of 2 to 3 inches.
Design also included upgrading taxiway edge lights to LED and replacing the entire taxiway lighting circuit, which had deteriorated to the point of failing. Like the runway rehabilitation work, Century West advocated on behalf of the Airport with the FAA to include the taxiway lighting circuit rehabilitation work with the runway project since so many other work elements were to be constructed concurrently.
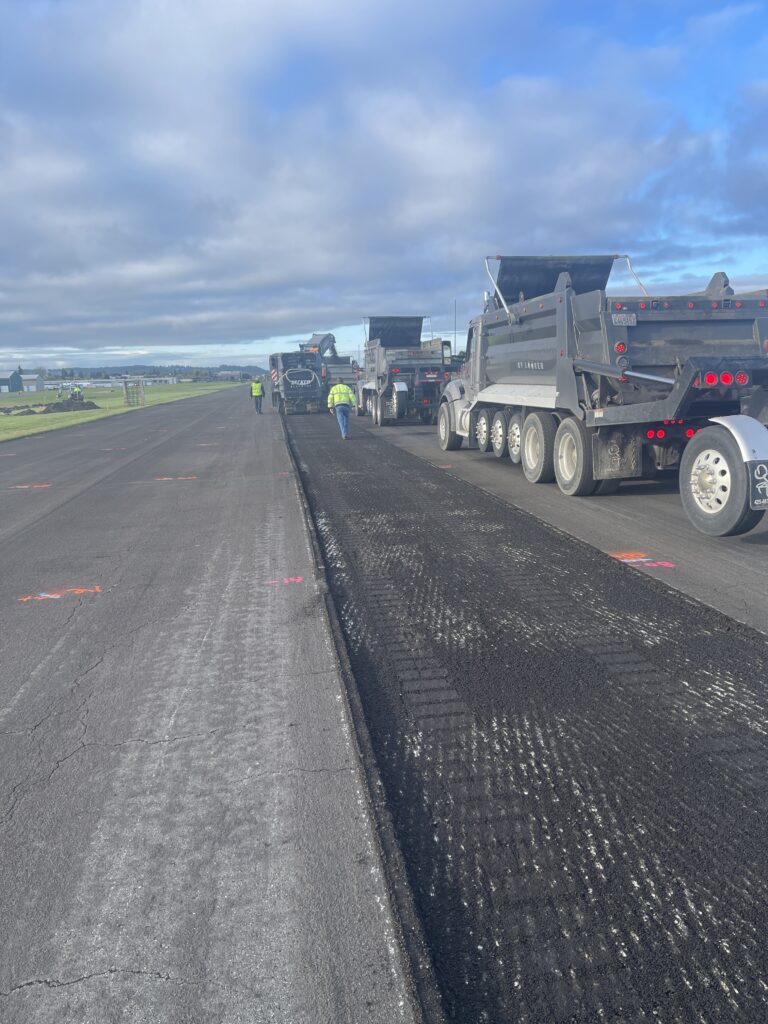
Another electrical improvement included removing the FAA-owned Visual Approach Slope Indicator (VASI) system and installing new Airport-owned LED Precision Approach Path Indicators (PAPIs). The VASIs had proven to be unreliable and no longer standard for operation. With the change in PAPI hardware, the Airport took over ownership of this system from the FAA, which will reduce the coordination required for their maintenance and operation. Combined with electrical improvements made during the previous runway extension project, all lighting at the Airport has been transitioned to energy-saving LEDs. Furthermore, the project was able to include sufficient spare lights, as allowed by the Airport Improvement Program Handbook.
Construction phasing became a hot topic as the project progressed toward bidding. Standard construction methods that would allow partial access to the runway would have resulted in a three-month construction duration that would have been highly disruptive to the flight schools, businesses, and small general aviation (GA) aircraft that operate at the Airport. Century West and the Airport instead decided on a phased approach with Phase 1 consisting of an initial four-week closure of the Airport for primary construction followed by Phase 2, which will be a three-day closure for installation of the PAPIs and final striping.
Public outreach was key in this process, and all credit goes to Airport Manager Tim Mensonides. Tim spearheaded the idea to broadcast to all tenants that the runway closure work for Phase 1 would be five weeks, despite the contract documents allowing a four-week closure. This message was carefully presented to allow for weather or construction delays that were likely to be encountered when trying to pave nearly 5,000 tons of asphalt in mid-May in the Puget Sound.
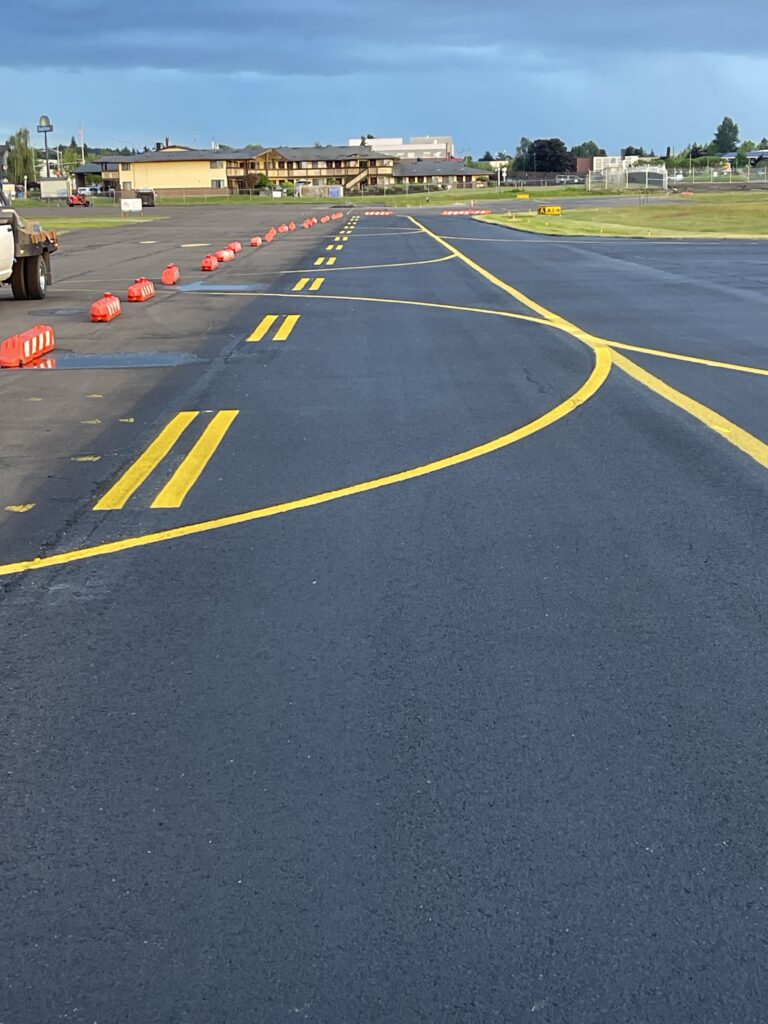
A lot had to go right to complete Phase 1 within the identified construction window. “We were really threading the needle when it came to getting the right grades during paving,” says Century West Senior Project Manager Greg Reince. To ensure plans were properly executed, Century West Construction Inspector Mike Perry was onsite for the duration of construction, and Century West Engineer-in-Training Jamie Suh provided extra eyes on the ground during paving. “We stipulated that the contractor had to have their surveyor take confidence shots to confirm it was done correctly,” explains Greg. “And I’m happy to report it came out as we hoped.”
Mike Perry brought 35+ years’ experience as an inspector—including more than 10 years at commercial service Airports—to the project and has a keen eye of what to look for when working in the airport environment. “Mike was a critical piece to the success of the project. In my 20+ years of Airport Management experience, Mike is easily the best inspector I’ve ever worked with,” said Tim.
Other elements of Phase 1, which was completed in May 2024, included a magnetic variation (magvar) change of the runway numerals, runway safety area grading and drainage improvements, fencing improvements, the inclusion of a new straight-in non-prevision instrument approach procedure, and a crack seal and fog seal of the Airport’s parallel Taxiway A. Phase 2 is anticipated to be completed in this fall.
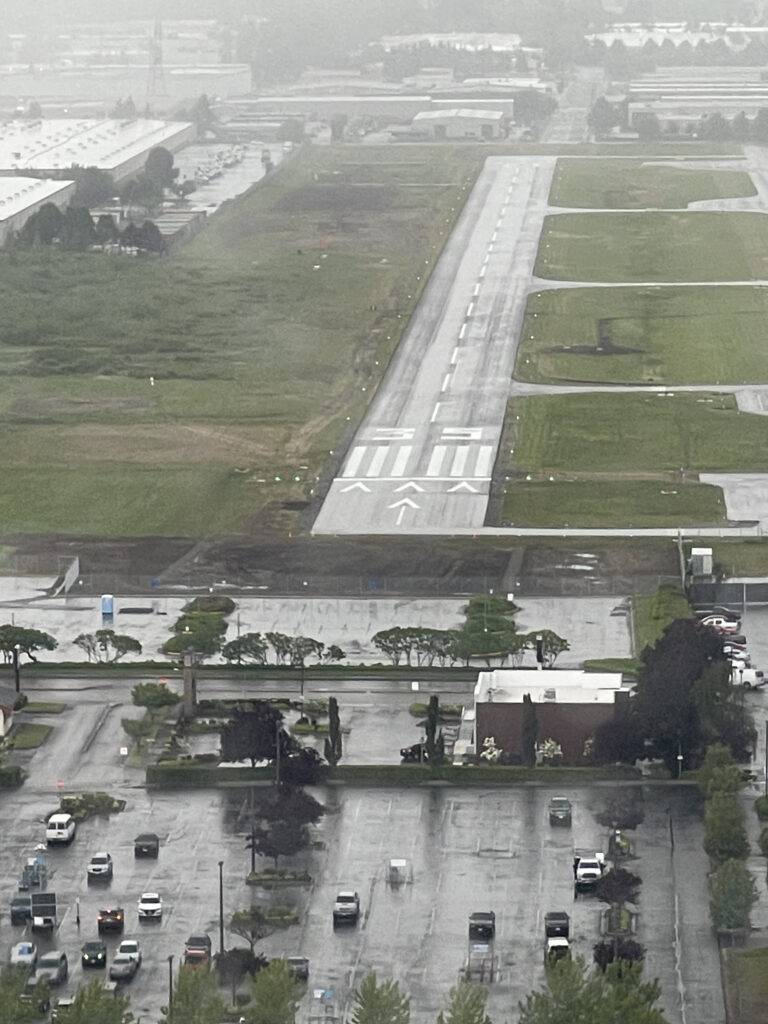
The approach procedure changes were made possible largely through efforts from Dave Parker, a member of the FAA’s Flight Procedures team. Again, Tim and Greg coordinated with the appropriate FAA channels to get the new approach procedure published—including the magvar change from 16-34 to 17-35—concurrent with the Phase 1 construction. Additionally, another curve ball that was thrown at the team was obstructions that had to be mitigated off each runway end for the new approach to be published. Century West and the Airport got to work, and all of the obstructions were mitigated prior the approach procedure being published. As a result, once the runway re-opened in May, the Airport had new, published runway numerals as well as an approach with lower minimums.
“This project was a game-changer for the Airport. It addressed significant pavement issues on the runway; improved safety by providing a fully compliant Runway Safety Area; and the new approach procedure will open markets the Airport did not have previously. The project could not have been completed without the close relationship Greg and I have. We talked daily during construction and at least weekly for the months leading up to the project. Airports of our size rely on the consultants to be an extension of Airport staff and ensure every aspect of the project is executed smoothly.”– Tim Mensonides, C.M. Auburn Airport Manager.
Century West is proud of the trust Airport staff place in our team to deliver cost-effective projects on time and on budget. This includes advocating for our clients with the FAA to ensure the right projects with the highest impact on smooth airport operations are in line for available funding. Our project managers and design teams take this responsibility to heart on all our airport projects.